KERANGWIN: Situs Slot Bonus New Member 100 Di Awal To Sangat Kecil Terbaru 2025
IDR 25.000 ( Aing Pocong )
KERANGWIN merupakan situs resmi slot bonus new member 100 di awal TO kecil, ambil promo bonus new member hari ini di situs KERANGWIN lewat depo 25. jadi jangan ditunggu lagi silakan langsung search di GOOGLE "KERANGWIN"
Quantity:
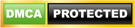